Verdant Tech Hub
/2025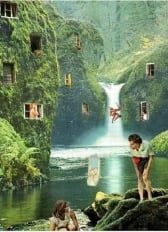
A stainless-steel cable net supports hundreds of native vine planters, wrapping flexible glulam-and-steel frames in a living curtain that cools interiors and sequesters carbon. Demountable CLT walls, under-floor services, and material-passport QR codes future-proof the incubator campus for rapidly evolving start-ups.
Project Gallery
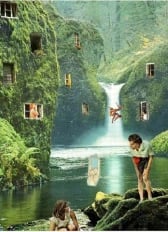
Timescales
The transition from polluted brownfield to ribbon-cutting occurred in 29 months: 12 months of remediation and geothermal bore-field installation, a nine-month structural build, and a six-month interior sprint.
The cable-net living façade of native vines was cultivated off-site for a full year and transplanted two weeks before opening, providing instant verdant coverage.
Long-term maintenance contracts with local horticulturists ensure vine establishment, sensor-based irrigation tuning, and pest management throughout the first growth cycle.
Objectives
Create a cradle-to-cradle workplace featuring reconfigurable modular spaces, QR-coded material passports for future deconstruction, and a live digital-twin model for operational optimisation.
Offer a 24/7 publicly accessible arcade, subsidised lab benches for early-stage start-ups, and cap annual energy use at 70 kWh/m² met entirely through on-site renewables.
Position the hub as a showcase where resident start-ups can prototype climate-tech solutions and host ongoing community education programmes.
Materials
A hybrid glulam-and-steel frame supports precast hollow-core slabs utilising concrete with 40% fly-ash replacement to slash embodied carbon.
A stainless cable-net façade carries lightweight planters filled with bio-char-amended soil, and interior CLT partitions are screw-fixed for tool-free relocation.
Every interior finish is catalogued in a QR-based material-passport database, streamlining future salvage and circular-economy reuse.
Challenges
Threading irrigation micro-tubing through façade mullions while guaranteeing watertight operable windows demanded bespoke gasket profiles and rigorous spray testing.
Frequent tenant spec changes required plug-and-play MEP cassette modules fed by flexible umbilicals, stretching just-in-time manufacturing tolerances.
Acoustic studies forced downsizing of the rooftop wind-turbine array, leading to additional PV pergolas over parking to maintain the renewable-energy target.