Skyline Innovation Park
/2021
Decommissioned shipping containers, stacked around an edible garden, form low-cost offices that power themselves with bifacial photovoltaics and second-life EV batteries. Open-source manuals, weekly horticulture classes, and free incubator units demonstrate circular-economy principles while catalysing inclusive entrepreneurship within a once-polluted railyard brownfield.
Project Gallery
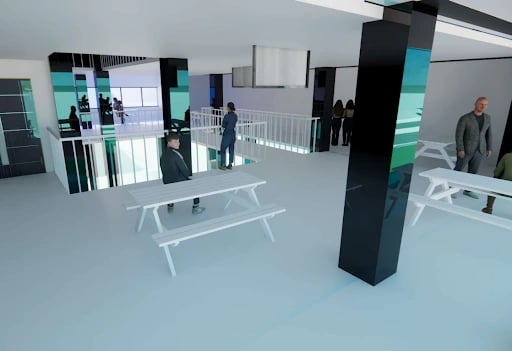
Timescales
Hazardous-material remediation occupied three months, after which eight intensive night-shift crane operations stacked 40 upcycled shipping containers into place.
Raised urban-farm beds were planted immediately to leverage the spring growing season, while a temporary expo pavilion created buzz six months before completion.
The entire build—including a rooftop bar and maker-space annex—wrapped in an impressive 17-month timeframe, well under budget.
Objectives
Provide ultra-low-cost, resource-positive incubator space, reserving rent-free units for founders from disadvantaged backgrounds.
Harvest more solar electricity and stormwater than the campus consumes annually, and publish open-source retrofit manuals documenting the entire process.
Achieve near-zero construction waste by crushing 91% of railyard rubble into recycled paving sub-base material for on-site paths and plazas.
Materials
Cor-Ten shipping containers are ceramic-spray insulated for thermal comfort, and CNC-cut window openings are repurposed as brise-soleil sunshades.
Elevated walkways utilise reclaimed hardwood sleepers, and gabion benches are filled with crushed on-site concrete ballast to close the material loop.
Bifacial PV arrays feed second-life EV battery banks, and interior walls are assembled from bamboo CLT panels finished with natural beeswax.
Challenges
Legacy creosote contamination necessitated full-coverage vapour barriers, and a late fire-code interpretation mandated a bolt-on external steel stair cage.
Uneven ballast sub-grades required floating resin-bonded gravel ramps to guarantee accessible paths across the site.
Continuous freight-line noise mandated high-spec acoustic glazing, stretching the budget until a local manufacturer sponsored the panels.